- Find the heat recovery loop that is shaped like the symbol for infinity (∞).
- Use a heat source with a similar temperature to improve efficiency! Find the best heating/cooling source
- Use the heat (latent heat) of steam
- Review temperature conditions and change operating conditions
- Think outside the box to aim for the best solution
Chemical Industry
Bleaching application for Kraft Pulp
Process overview
There are two processes: heating the ClO2 aqueous solution with steam and cooling the water supplied to the chiller unit with electricity.
- Improvement effect
- Water supplied to the chiller unit is cooled by the ClO2 aqueous solution from the ClO2 tank, and therefore heat can be recovered. ClO2 aqueous solution that is heated with steam can be heated with hot water recovered from white liquor.
The power consumption of the chiller unit is reduced and heated steam is not required.
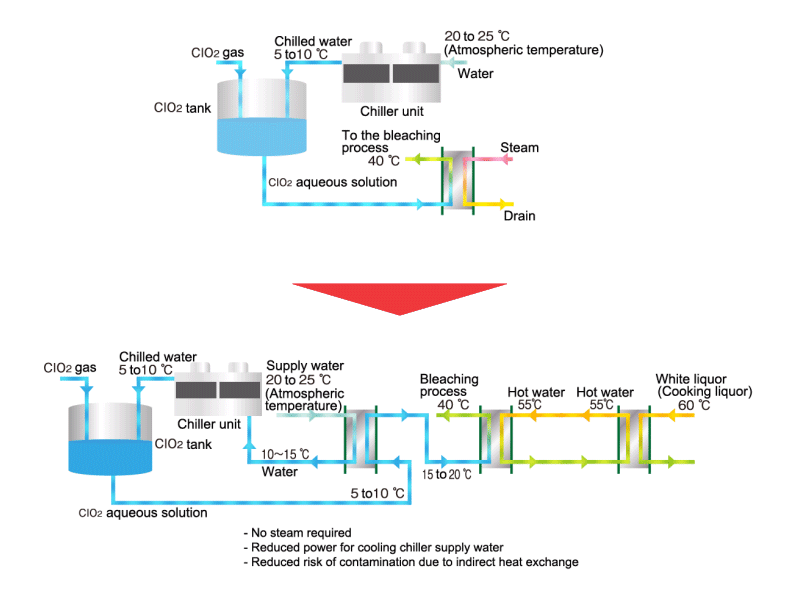
Multiple effect column evaporator
Process overview
This is a standard triple effective evaporation column, which is traditional and well-known process to reduce the steam consumption to approximately 1/3 from single column. Process is almost perfect, but something are still hidden.
- Improvement effect
- The wasted vapor temperature from the 3rd column is so low that is usually ignored. But PHE is still applicable of its high efficiency. In this case, wasted vapor is used for pre-heating of the process feed. Additionally, new heat recovery network can be created by the infinity loop principle.
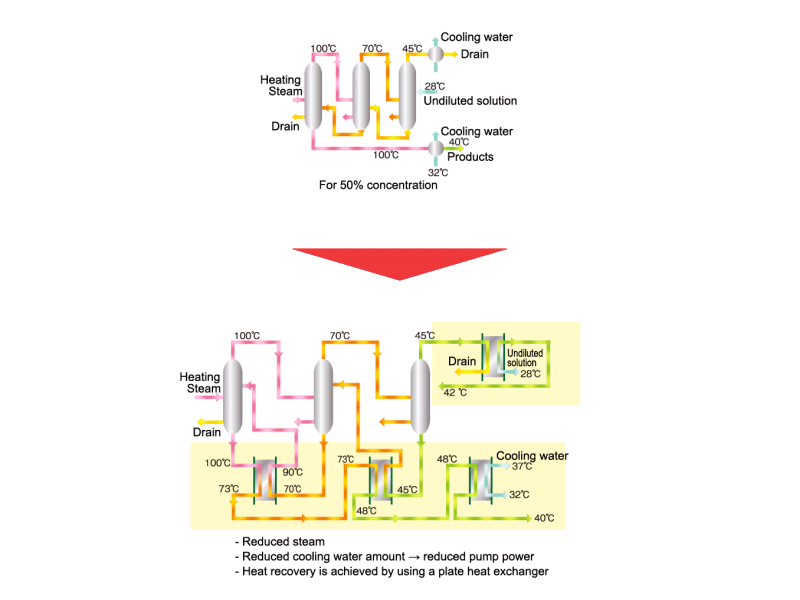
CO2 Recovery
Process overview
In this process, the low-temperature lean amine in the absorption column absorbs CO2 gas and becomes rich amine. This rich amine is heated, CO2 gas is released from the regeneration column, and it becomes lean amine. It is then cooled and returns to the absorption column, and the CO2 absorption/emission cycle is repeated.
- Improvement effect
- High-temperature lean amine from the regeneration column is cooled and sent to the absorption column. Low-temperature rich amine from the absorption column is heated and sent to the regeneration column. By exchanging heat between high-temperature lean amine and low-temperature rich amine, the amount of steam in the regeneration column can be reduced.
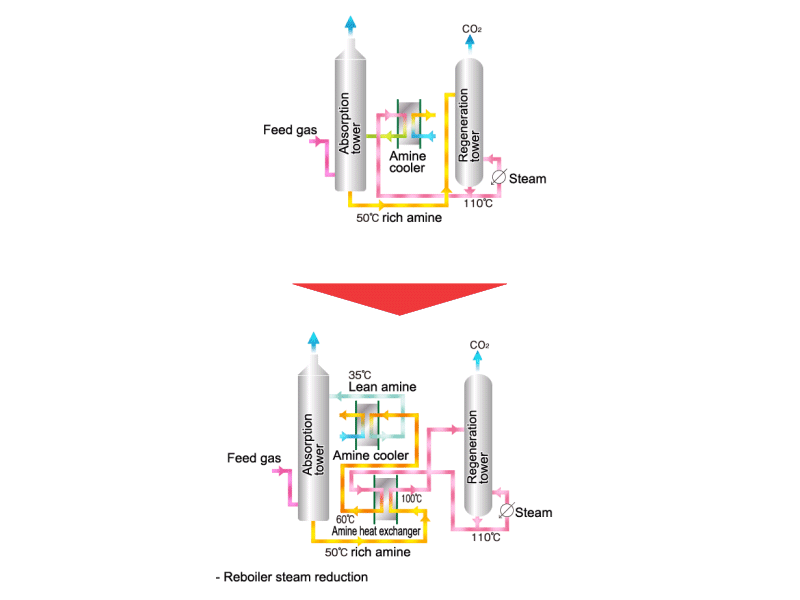